Produkte
Wie löse ich Fertigungsaufgaben?
Hier findest Du kurze Fertigungsrezepte aus der Community – diese Lösungen haben andere Nutzer erfolgreich umgesetzt.
Rezepte
Für ein Lokomotivmodell der preußischen Dampfschnellzuglokomotive S10 im Maßstab 1:16 habe ich Radgussformen hergestellt . Dabei wurde die Gussform für den Radstern als Laserteil realisiert. Die Radreifen und die Kurbelwangen der gekröpften Achse sind ebenfalls Laserteile.
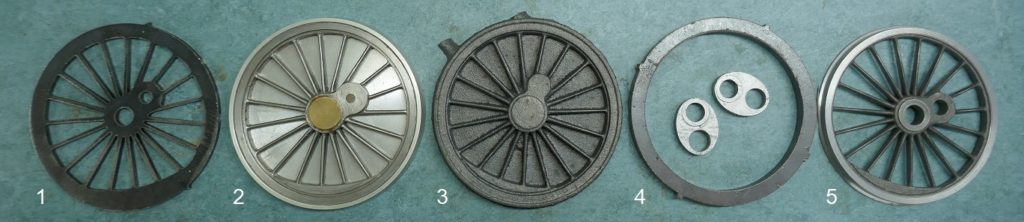
Die Bilder zeigen die Abfolge bei der Herstellung:
1. Gelaserter Radstern für das Gussmodell. Der Sturz wird auf der Fräsmaschine hergestellt, die Speichen dann in Form gefeilt.
2. Zusammengebautes Gussmodell, zur Abformung in Sand.
3. Gussrohling, dieser wird durch Abdrehen auf Form gebracht.
4. Gelaserter Rohling für den Radreifen. Dieser wird auf den Radkörper aufgeschrumpft. In der Mitte die gelaserten Rohlinge für die Kurbelwangen der Kropfachse.
5. Fertig montiertes Rad mit profilierter Lauffläche.
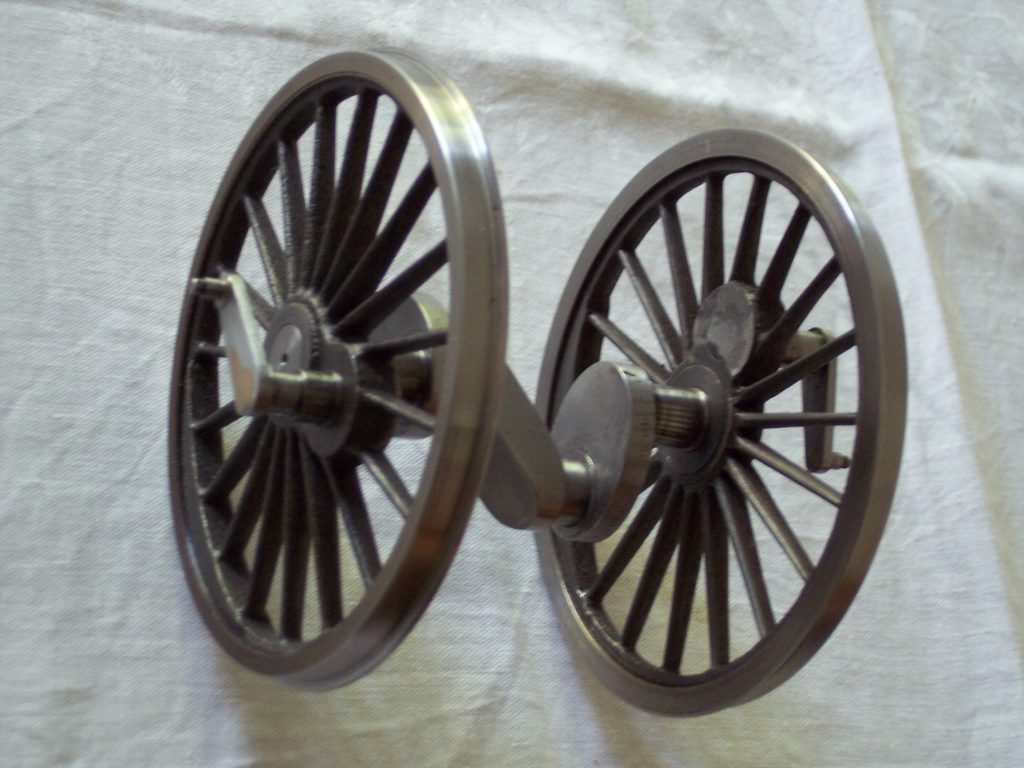
So sieht die fertig montierte Kropfachse aus, mit eingepressten Treibzapfen und hart aufgelöteter Gegenkurbel.
mit gezunderter Oberfläche / walzblau als individuellen Zuschnitt mit beliebiger Kontur – auch schwierige Fälle.
Wofür braucht man das?
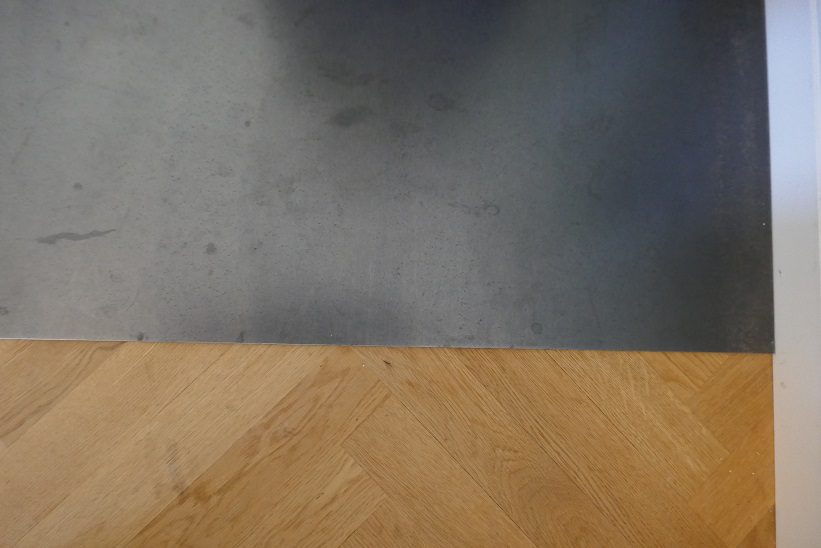

Vorlagen zum Nachproduzieren:
Die Zeichnungen können durch Anklicken im teknow-Designprogramm geöffnet werden. Sie sind dort auch anpassbar.
Feuerkorb “Pentagon”, Abmessungen 321 x 321mm, 500 mm hoch. Es werden je zwei Seitenteile und eine Bodenplatte benötigt.
Material ist Corten A in 4 mm.
Sofern der Fußboden, auf dem der Kamin oder Ofen steht, nicht feuerfest ist, wird eine nicht brennbare Unterlage benötigt. Diese verhindert, das beim Nachlegen des Brennholzes herausfallende Funken einen Brand auslösen. Ein schönes Material für so eine Unterlage ist unbehandeltes Schwarzblech. Mit dem teknow-Designer kannst Du das Blech individuell zuschneiden, mit beliebiger Kontur und Ausschnitten, z.B. für die Luftzuführung. So lässt sich das Blech auch in schwierigen Fällen, wie schrägen Wänden und Vorsprüngen, genau anpassen.
Was ist Schwarzblech?
Schwarzblech ist ein nicht entzundertes Grobstahlblech (ab 3 mm Stärke). Der “Zunder”, das Eisenoxid auf der Oberfläche, entsteht beim Walzen des glühenden Blechs. Es entsteht eine lebhafte graue bis blaue Oberflächenfärbung, die auch als walzblau bezeichnet wird. Jedes Blech hat eine individuelle Farbstruktur. Die Oberfläche ist eher metallisch schimmernd als glänzend.
Das Blech kann durch Produktion und Zuschnitt leichte Kratzer aufweisen, besonders an der Unterseite durch die Auflage auf die Lasermaschine. Daher ist es wichtig, die Zeichnung seitenrichtig zu erstellen.
So geht es:
Die Funkenschutzplatte muss die brandgefährdeten Flächen seitlich um 300 mm, an der Öffnungsseite um 500 mm vor dem Ofen abdecken. Falls der Ofen drehbar ist, muss das entsprechend berücksichtigt werden. Im Zweifel den Schornsteinfeger fragen, der die Anlage am Ende auch begutachten und abnehmen wird.
Dann fertigst Du am besten eine Handskizze der Platte an. Dazu wählst Du eine geeignete Ecke als Nullpunkt aus, und trägst die Maße von da ab in mm ein. In den meisten Fällen geht das sehr einfach. Hier ist ein Beispiel für einen schwierigeren Fall.
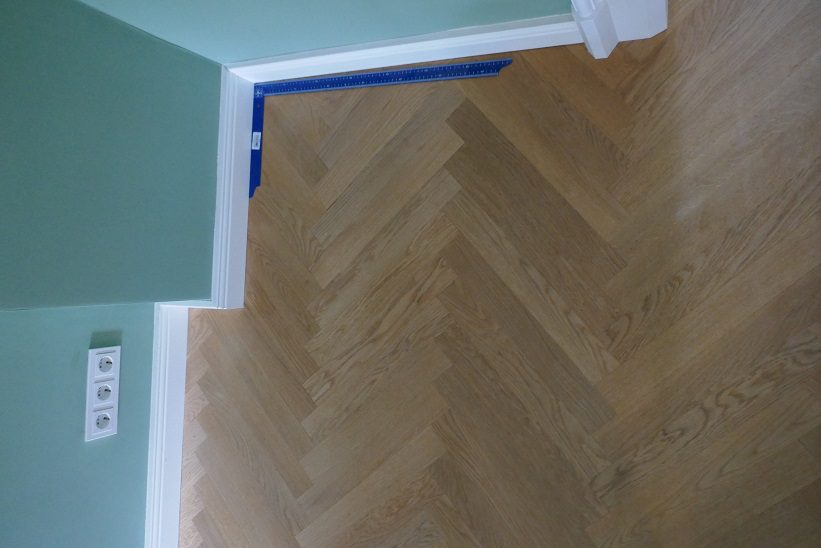
So sieht die Ecke aus. Die Wände stehen nicht genau rechtwinklig. Der Ofen hat eine Grundfläche von 350 x 350 mm², daher müsste die Platte 950 mm breit sein. Die Wand oben im Bild ist aber nur 850 mm lang – man muss also dem Sockel des Türrahmens ausweichen.
Zuerst messen wir die Ecke sorgfältig aus und fertigen eine Papierskizze an. Als Nullpunkt habe ich die Ecke rechts hinten genommen. Alle Maße werden in mm angegeben.
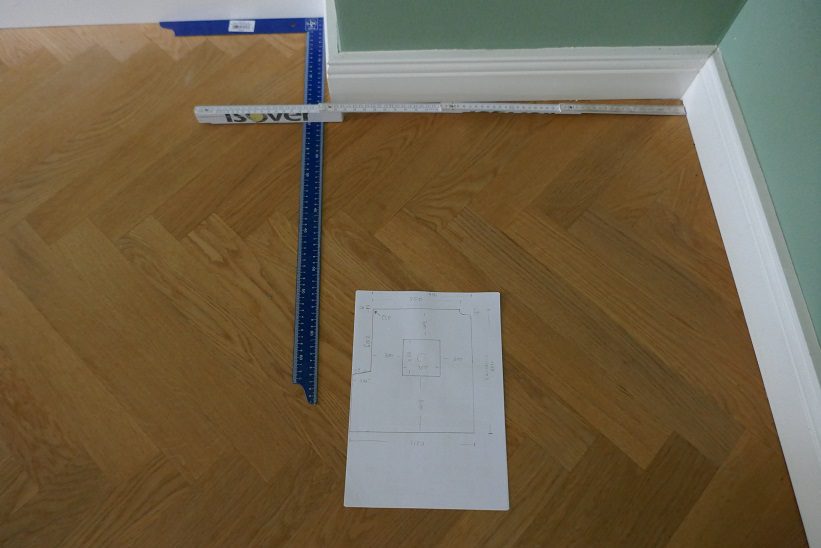
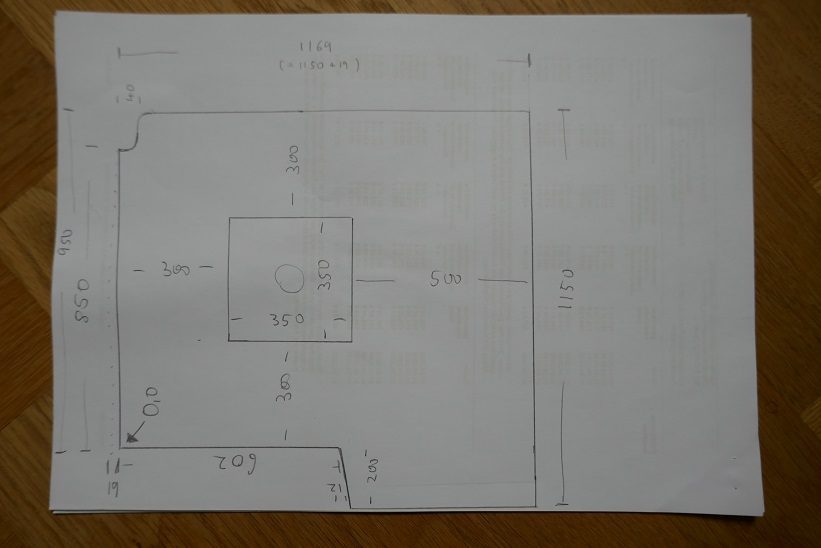
Dann überträgst Du die Skizze ins teknow-CAD. Wie das geht, ist in der Hilfe und in den Videos genau erklärt.
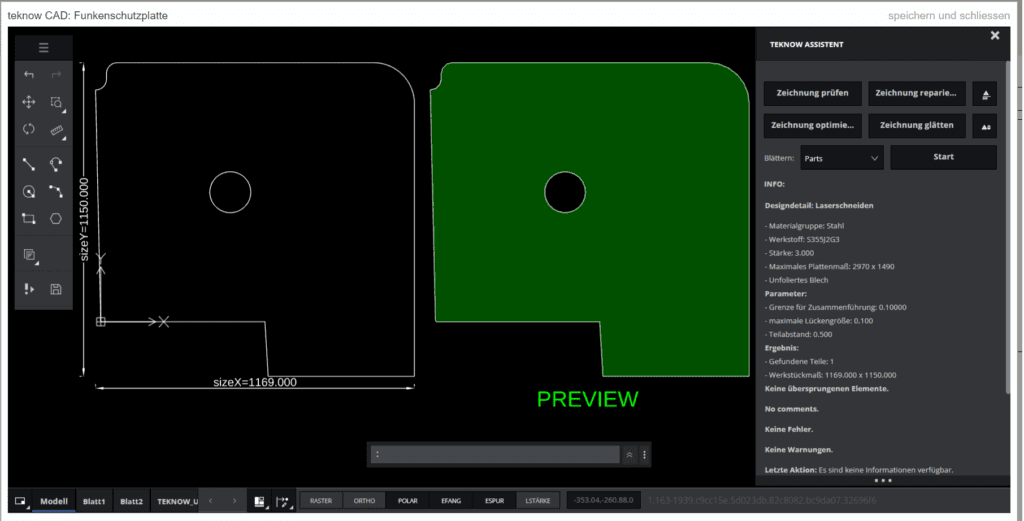
Nach der Lieferung:
Schwarzblech rostet, wenn es naß wird. Im Innenbereich kann es unbehandelt verwendet werden, sofern es mit Wasser nicht in Kontakt kommt. Nach Lieferung solltest Du die Kanten kontrollieren und ggf. mit etwas Schmirgelpapier nachrunden, dann das Blech einmal reinigen – einfach mit Schwamm oder Tuch, warmen Wasser und Spülmittel abwischen. Das Blech danach gründlich trocknen, besonders auch die Schnittkanten. Das Blech kann geölt oder lackiert werden, vielleicht angepasst an den Untergrund, wie zum Beispiel geöltes oder lackiertes Parkett. Das Öl (z.B. Leinöl, Ballistol) sehr dünn auftragen und trocknen lassen. Lackiert werden kann mit einem Acryl-Klarlack für Metalle (seidenmatt, nicht wasserbasiert). Die lackierte Oberfläche wird gegenüber glühenden Kohlestückchen empfindlicher sein als die geölte.
Rahmenwangen, Querverbinder und Verbindungsteile für Lokomotivmodelle lassen sich ideal mittels Laserschneiden produzieren. Das Gesagte gilt natürlich genau so für andere Antriebsarten, wie akkugetriebe Modelle.
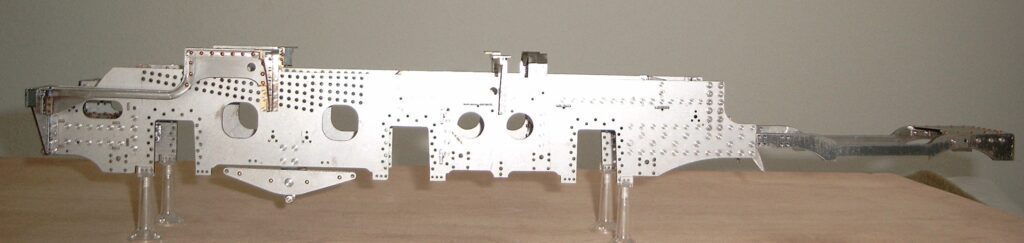
Das Beispiel zeigt den Blechrahmen eines Modells der pr. S 10 im Maßstab 1:16. Alle Bohrungen wurden gleich mit ausgelasert, dazu an einigen Stellen Zapfen und Schlitze zur exakten Ausrichtung der Bleche. Das Rahmenblech ist 3 mm stark, der vorgeschuhte Barrenrahmen besteht aus durch Fräsen weiterverarbeiteten 10mm starken Blech. Die gebogenen Unterzüge, die Konsolen und die Ausgleichshebel sind ebenfalls auf Basis von Laserteilen entstanden.
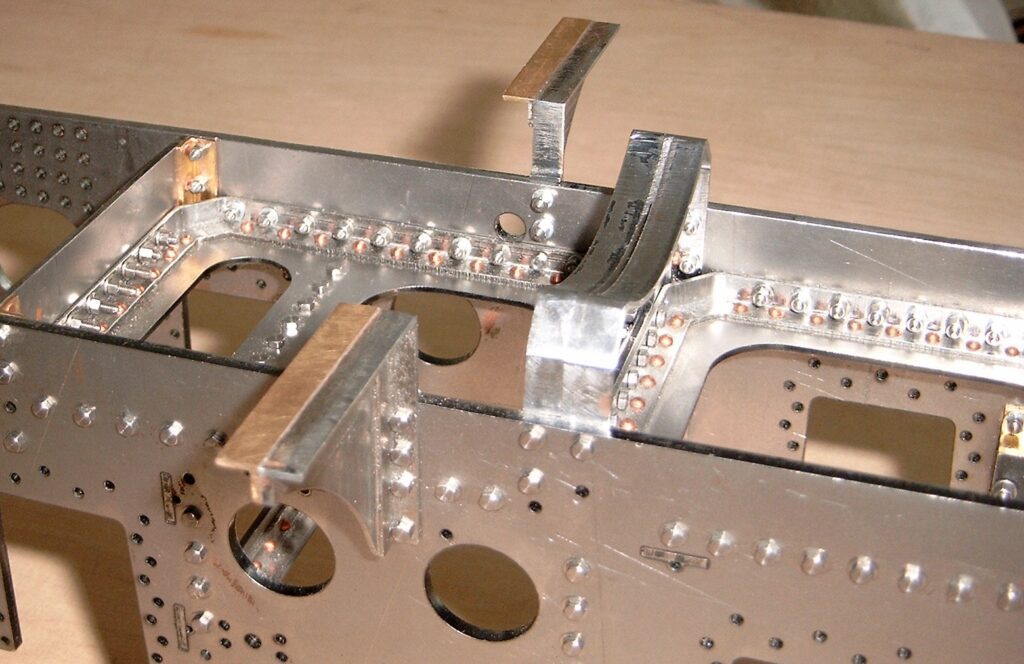
Das Detailbild zeigt die Rahmenversteifung mittels Blechen, die über Winkelrahmen miteinander vernietet und verschraubt sind. Die Bleche wurden direkt wie ausgelasert verwendet.
Die Rohlinge für die Winkelrahmen und die Kesselauflage bestehen aus 6 mm Blech, anschließend wurden die Winkel durch Ausfräsen hergestellt. Teile gleicher Stärke wurden jeweils durch Stege zusammengefasst. Das ist in der Regel günstiger. Bei Teilen, die durch Fräsen weiter bearbeitet werden sollen, vereinfacht das bei passender Anordnung die Aufspannung.
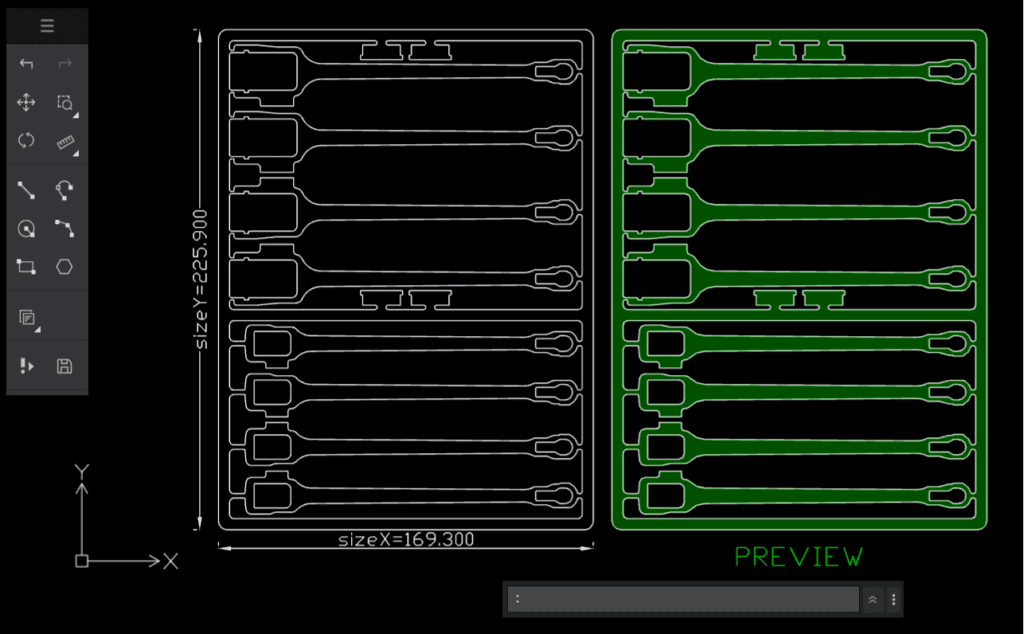
Die Zeichnung zeigt die zu einem Block zusammengefassten äußeren und inneren Treibstangen, sowie die Verschlüsse der inneren Treibstangenköpfe.
Die Rohlinge für viele andere Teile eines Live-Steam Modells lassen sich ebenfalls gut mittels Laserschneiden produzieren. Hier einige Beispiele.
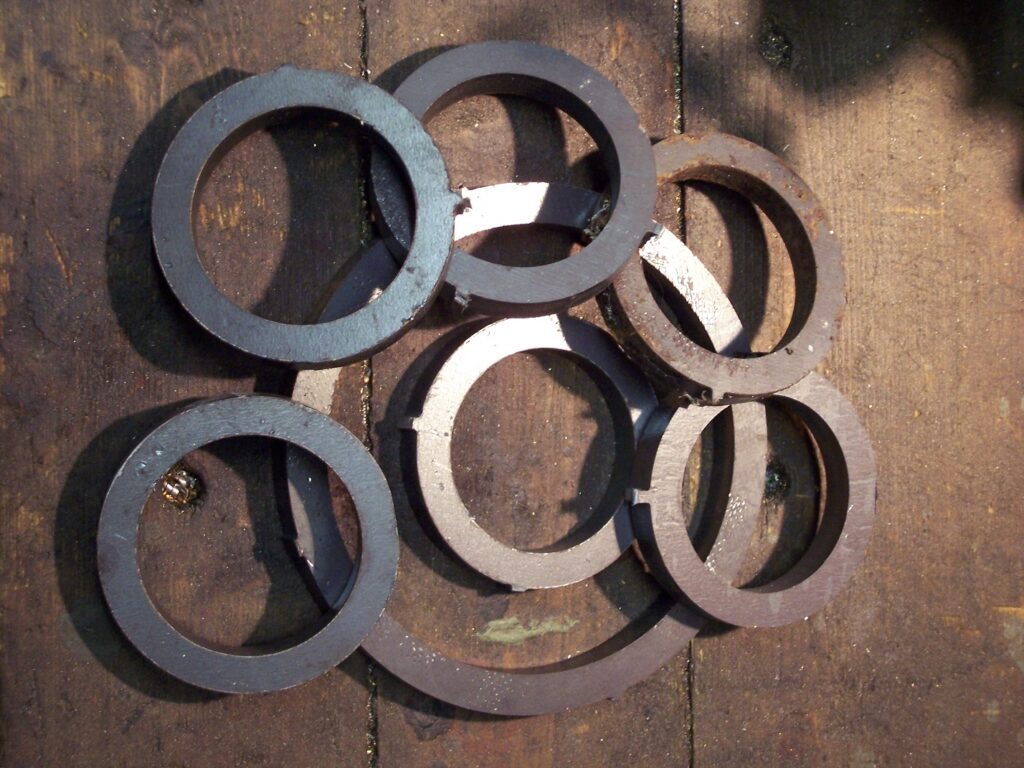
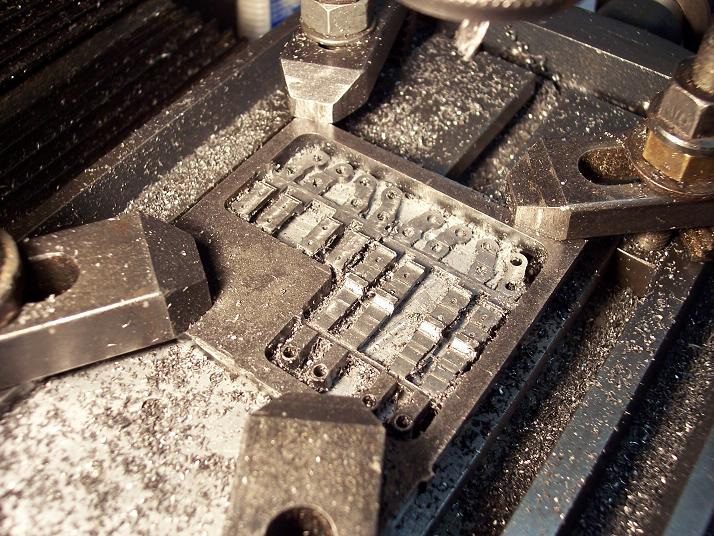
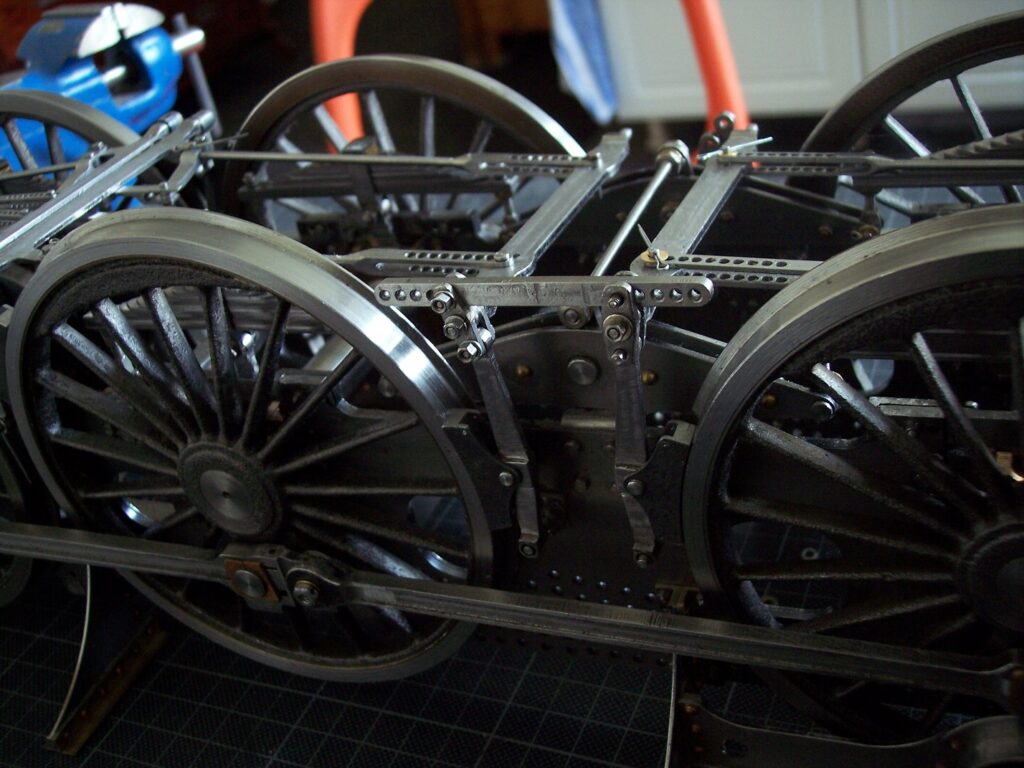
Links: Die Rohlinge für die Radreifen bestehen aus 10 mm Stahl.
Mitte: Die Rohlinge für die Treib- und Kuppelstangen sowie die Steuerungsteile lassen sich in einem Raster so anordnen, dass das Aufspannen auf der Fräse zum Fertigbearbeiten erleichtert wird. Das Bild zeigt die zusammengesetzten Voreilhebel, die auf der Fräse fertig bearbeitet werden.
Rechts: Bremsklötze, Bremshebel und Ausgleichsbalken auf Basis von Laserrohlingen.