With plasma fusion cutting, the workpiece is cut out with an electric arc. The arc is created by blowing a gas through a nozzle onto the workpiece. An electrode is located inside the nozzle and an arc is struck between this electrode and the electrically conductive workpiece. The arc ionizes the gas jet to form a plasma. Temperatures of 30,000 ° C are reached in the arc. The plasma jet melts the material in the kerf and at the same time blows out the liquid material.
The pricefor a workpiece is made up of a share for the cutting time (depending on the material, thickness, cutting length, number of grooves), the material price and the fixed costs. If there are several identical workpieces, the fixed costs are only incurred once, i.e. the price per workpiece decreases considerably, depending on the geometry.
Production examples
30mm S355J2 + N with mill skin 30mm S355J2 + N detail 30mm S355J2 + N blasted
Plasma cutting creates almost right-angled and largely post-processing-free cut surfaces. The heat input during cutting results in a hardening on the cut surface, but this is less than with oxy-fuel cutting. The formation of burrs and roughness of the cut edges increase with the sheet thickness, see the following pictures of the cut edges. We sandblast the surface of the sheet metal.
Images of the cut edges
Cutting edge, un-blasted Cutting edge steel, blasted Detail Steel 30mm S355J2 + N
Procedure
Create a new workpiece and select “Plasma cutting” as the method. The only material available is steel S355J2 + N. Then you determine the strength.
You draw the workpiece in the teknow Designer. White lines indicate the outer contour or openings. Yellow lines are interpreted as engraving lines. You can use the wizard to check that all design rules have been followed. The price for a single workpiece will be displayed after you have closed the designer. We create a production file from your drawing. We manufacture according to DIN ISO 2768-m / EN ISO 9013-342. White lines indicate the outer contour or openings. You can use the wizard to check that all design rules have been followed. The price for a single workpiece will be displayed after you have closed the designer. We create a production file from your drawing.
Advantages of the procedure
• No tool costs
• Individual parts possible
• short production time
• flexible geometry can be produced
• medium and larger material thicknesses
• Smooth cuts, no need of post-processing
• Low heat input and material distortion
• high cutting speeds
• Cheaper than laser and water jet
Design rules
The smallest hole diameter must be at least equal to the selected material thickness, the smallest web width equal to twice the selected material thickness. Here, too, the wizard provides appropriate information (marked as a warning). If all rules are observed, the production takes place with tolerances according to DIN ISO 2768-m / EN ISO 9013-342. Here, too, the wizard provides appropriate information (marked as a warning). Burned holes are slightly conical with larger sheet metal thicknesses. This means that the diameter on the upper side of the sheet corresponds exactly to the specification, but the diameter on the underside of the sheet is smaller. If this is relevant for the component, the bore diameter should be selected 1 to 2 mm larger. If all rules are observed, production takes place with tolerances according to DIN EN ISO 9013.
The metal sheets are mostly 2500 x 6000 mm², larger workpieces lead to an error message.
Materials
Steel
S355J2 + N (1.0577, ST 52-3) is an unalloyed, stronger standard structural steel for general applications. Very easy to weld. Rust protection is required outdoors.
Available in thicknesses of 20, 25, 30, 35 mm.
Finally a look into the production:
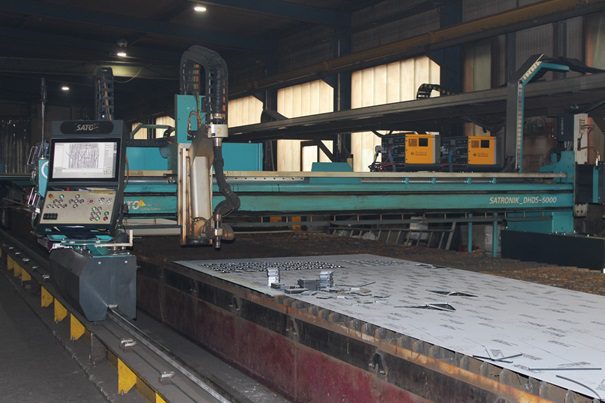
A numerically controlled machine moves the cutting beam over the sheet.
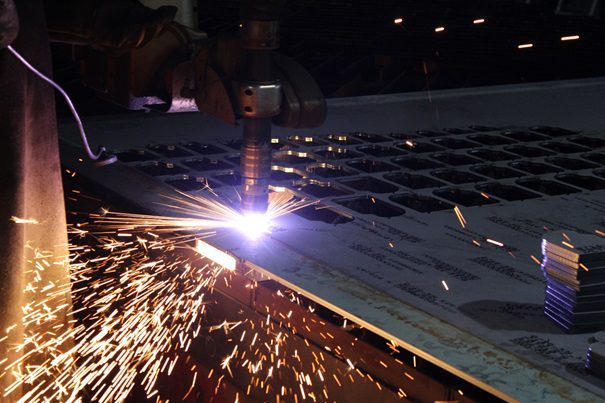
A plasma cutting machine when cutting workpieces.